Hot Dip Galvanizing
The only process that chemically bonds steel with molten zinc to form one of the most durable, resilient and maintenance free coating systems available. High-quality hot dip galvanising process.
Process & Capabilities
The Galvanizing Process
Size Capability
Our galvanizing bath in Elgin measures 10.5m long x 1.1m wide x 2.5m deep which allows processing of steelwork of up to 15m in length and 1.05m in width.
Our galvanizing bath in Cumbernauld measures 7m long x 1.2m wide x 3m deep which allows processing of steelwork of up to 10.5m in length and 1.15m in width.
The width of an item is usually the main determining point on whether an item is suitable for galvanizing. The metal will expand as it is heated in the zinc bath therefore an expansion tolerance must be allowed for at the design stage.
The maximum lifting capacity including equipment is 4 tonnes at both plants.
Watch Our Videos About Galvanizing…
Hot Dip Galvanizing Benefits
Projects we are proud to have been involved in …
Roseisle Distillery
The Edinburgh Military Tattoo
Edinburgh Sculpture Workshop
What can you galvanize?
Anything that is made from mild steel and fits within our sizes capabilities.
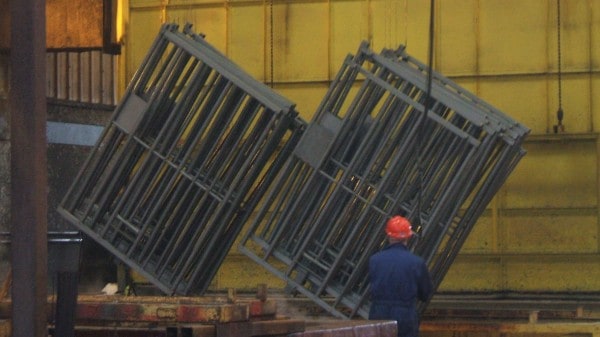
Agricultural Equipment
Moving parts such as drop bolts and slip bolts can be accommodated by ensuring that sufficient clearance is designed into the fabrication.…
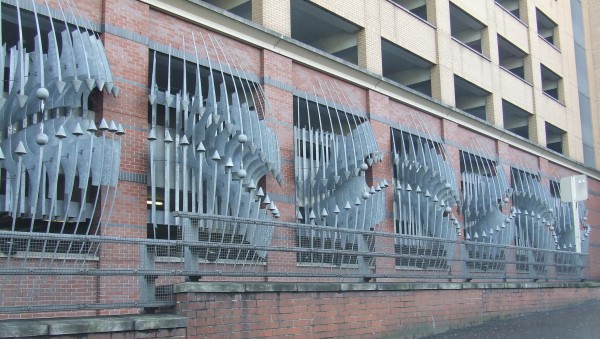
Creative Steelwork
Creative designs often contain intricate sections that can prove problematic to paint and maintain. By opting to hot dip galvanize all surfaces will receive an equal coating whether they are hidden, hard to reach or even internal.…
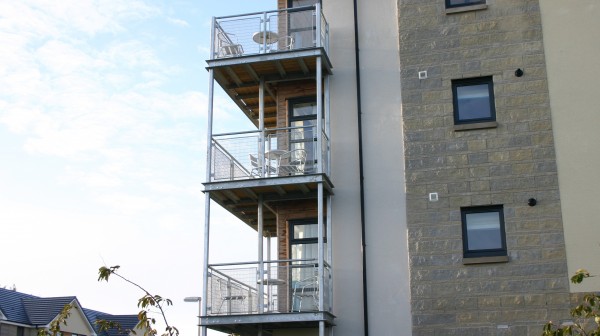
Balconies
To keep looking good, and functioning as intended, it is imperative that corrosion protection is the main priority when specifying a balcony.…

Whisky Distilleries
Whether it be mashing or maturing, whisky distilleries suffer from high moisture content. By choosing to have the steelwork galvanized, costly downtime to carry out painting is eliminated.…
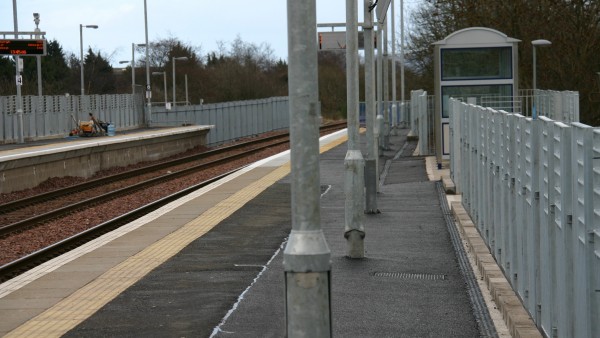
Lighting
Lighting units are a great candidate for galvanizing, as the posts benefit from being coated on both the inside and out.…
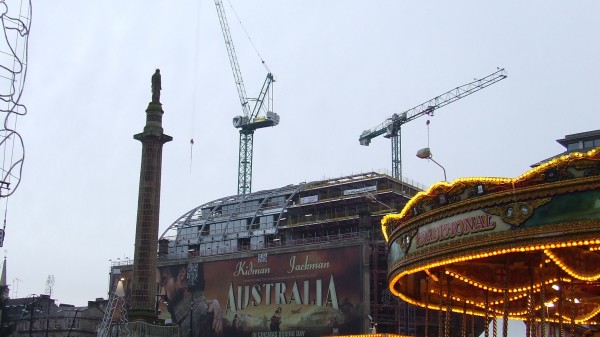
Structural Steelwork
By galvanizing steelwork before it reaches site it will not only benefit from a long hassle free life but it will also be protected from impact damage during erection.…
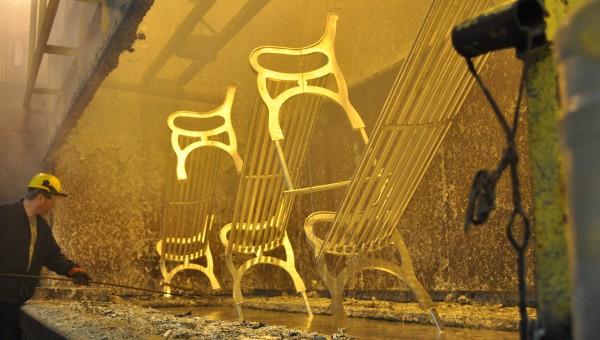
Street Furniture
Benches have a hard enough life, give them a break get them galvanized!…
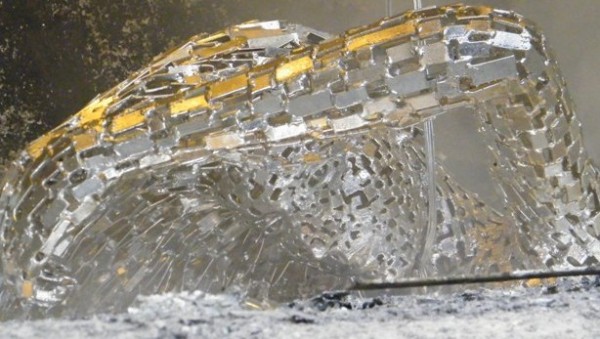
Sculptures
Steel sculptures look great but can be difficult to maintain due to all the intricate details that need to be protected from going rusty. By immersing the sculpture in molten zinc all surfaces are coated equally.…
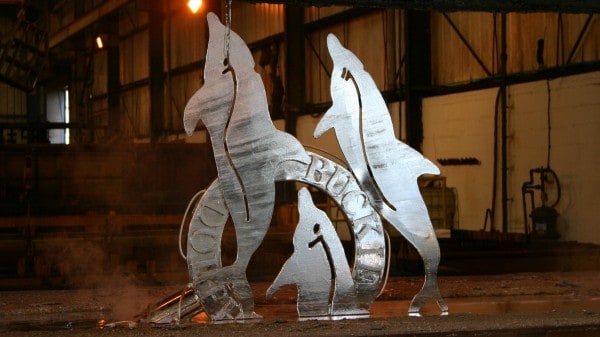
Signage
There’s nothing worse than a rusty sign with the paint peeling off – just galvanize and never have to worry again. Give us a call to find out about our refurbishment service.…
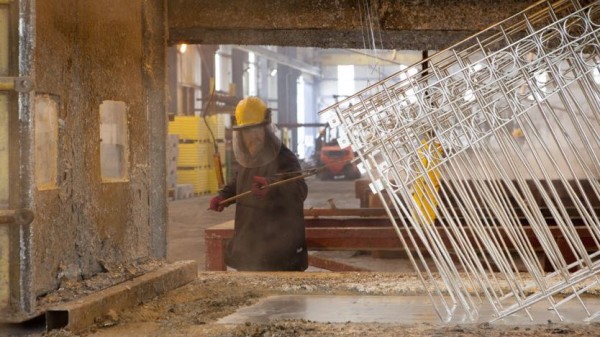
Fencing
Palisade, bowtop, security, chainlink, decorative….there are millions of miles of fencing in the world, galvanizing is the easiest and best way to give it a long, maintenance free life.…
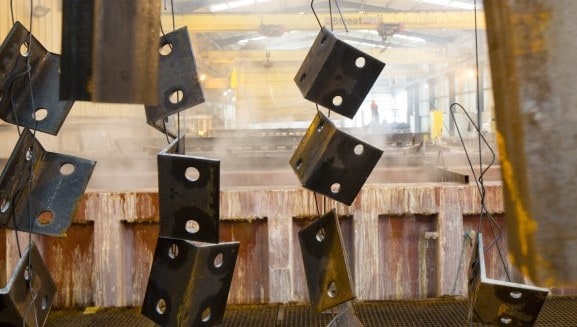
Brackets
A small but integral part of many fabrications – hot dip galvanizing provides a long, maintenance free life.…